
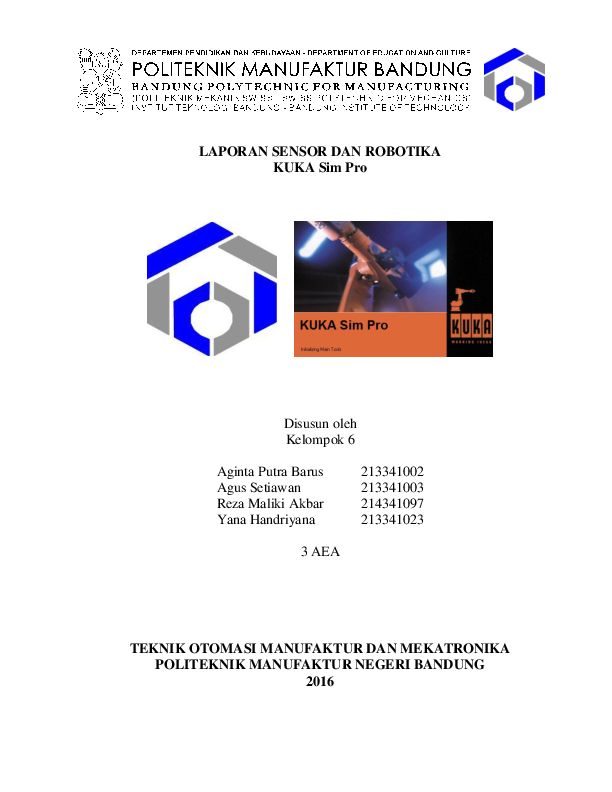
Maybe the problem is because I use a linear movement, but I don't think so.Ģ) What about collisions? Even if I connect an object to KUKA|prc and I define " check for collisions" in a corresponded setting, it gives me almost nothing. I imagine there should be some way to tell robot to compensate the positioning using the other joints, but I cannot figure it out. I tried to define it as a mean point of a geometry so that the tangentials were pointed at a center of the geometry also I tried to move the point far away so that the tangentials were almost parallel. I think this all is because I really have no idea about the orientation point
#Kuka sim pro tutorial pdf how to
So, the question is how to solve this problem. For example, last time it reached -349° at A6 and tried to go further but it blocked itself, due to the movement limits. Depending on situation, the robot blocks different joints (usually A4 or A6), but anyways I cannot finish the drawing. I even tried to redefine the starting point of the movement. Look the attached pictures to understand what I mean. But when I try to run it with KUKA, it comes to a border condition and blocks the movement. But in case of a closed geometry (I chose a snail as a geometry) when I run simulation of movement, everything goes well, too. Well, here are the problems I am stuck with:ġ) When I draw any curve, everything goes well. I added the table surface in order to check for collisions. I created the control program, using your Custom_tool tutorial as a basis. I want it to be aligned to X tool tip axis, i.e. Therefore I created a mesh of my tool, imported it, defined the position of the tool. I want the robot to draw using a sharpie. So, I decided to go further using custom tool. Everything works quite good, the KRL codes that I got from your tutorials are going perfectly. I have studied all the tutorials you'd provided (thanks a lot, they are pretty clear) and I have already calibrated the robot following your instructions ( ). I am preparing for my project at university and getting familiar with KUKA|prc and application of it using KUKA KR16. The fact that B is always 90 probably means that you've got only vertical positions (B is the rotation around the local Y-axis). 010, an explanation is in the KUKA Expert Programming Manual, should be on the included CD, see also the graphic below that shows the different ways how a robot can reach a defined position. Regarding the A4 problems you can try to set the first position as a PTP movement with a specific Status value - e.g. So the KUKA|prc solver is made to best approximate the way KUKA robots behave. you put the KUKA|prc-generated KRL file there and can execute it virtually.

The most accurate simulation you are going to get is via the combination of KUKA SimPro and OfficeLite, which is a virtualized robot controller, i.e. Post in the forum or get in touch with if the problem persists.įirst of all, this may of course be a bug, but I cannot diagnose this without the file (and preferably the robot).īasically, it's important to consider that there is no "official" KUKA kinematics solver available for third-party software.
#Kuka sim pro tutorial pdf update
Members are encouraged to use the most recent version of KUKA|prc - we usually update the software at least once a month. You can enable LIN Interpolation in the settings to spot errors in between LIN movements. KUKA|prc only calculates the programmed positions, but there can be out-of-reach positions in between as well. when you manually skip an unreachable position via the smartPAD/KCP. Do not depend on any information that comes AFTER an unreachable position. The simulation is only accurate until the first point that is out of reach. If you change them back to default, make sure that there are no mechanical stops installed. It is possible to set custom axis limits, which differ from the standard robot setup. Please refer to the sticky post on top of the forum: tool and base have to use the same number and XYZABC value. EDIT: As this is post is viewed very frequently, here is some useful troubleshooting advice:įor an accurate simulation, the physical and digital robot have to be synchronized, i.e.
